Non-Destructive
Testing
Services
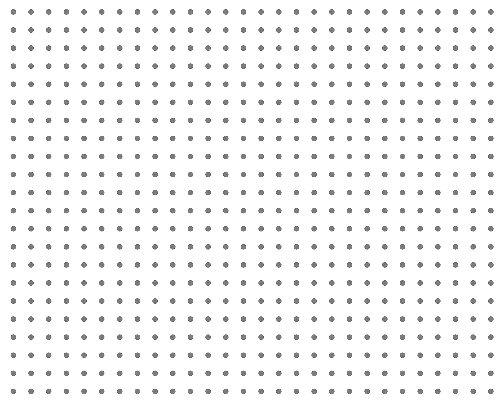
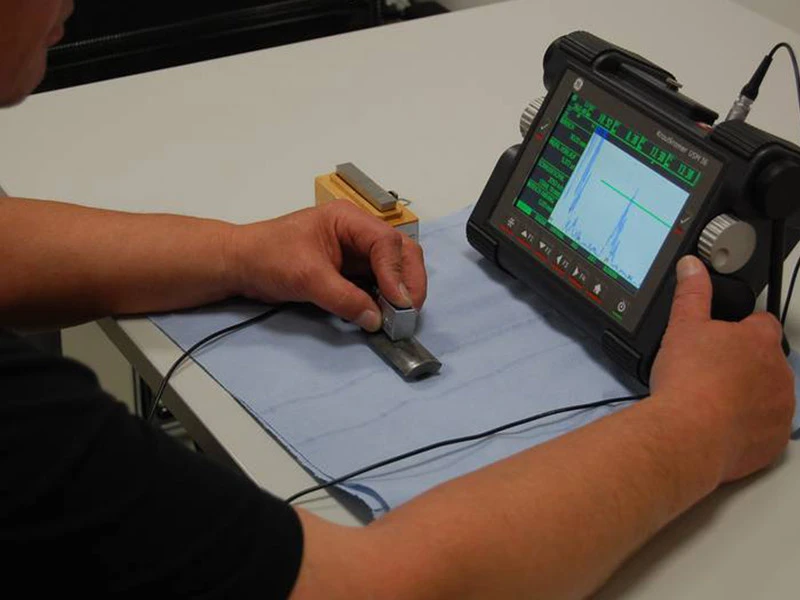
Providing reliable services with competent personnel and equipment
Globe Inspection & Engineering Consultancy is a trusted provider of comprehensive Non-Destructive Testing (NDT) services. Our expertise helps us to offer a wide range of NDT inspection services tailored to meet your specific needs.
As an experienced service provider of NDT services, we understand how important the structural integrity and reliability of your assets are. So, with the help of our highly skilled technicians, we employ cutting-edge techniques to find out the flaws and defects. We do this with no damage to the tested components.
Our NDT services cover several materials and structures, which include weldments, castings, forgings, and so on. Also, we cater to various industries, which include manufacturing, construction, aerospace, and others through our Non-Destructive Testing (NDT) services.
For all your NDT needs, we deliver reliable and accurate results and serve you as a trusted partner. And this is possible because our technicians undergo rigorous training and stay updated with all the industry advancements, ensuring the highest service quality.
Globe Inspection & Engineering Consultancy can provide trained and qualified manpower on a short-term and long-term basis. Our personnel are trained and qualified to comply with national and international standards such as ASNT NDT Level II & Level III.
Our NDT services include the following
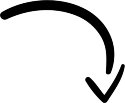
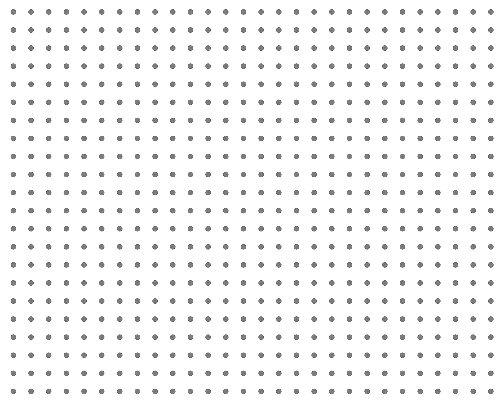
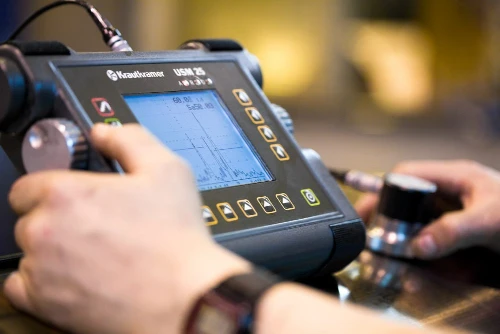
Ultrasonic Testing (UT)
Ultrasonic (UT) inspection is performed on various weld configurations when the radiographic examination is not feasible due to factors such as geometry and limited accessibility to both sides of the inspection area. Additionally, Ultrasonic Testing (UT) is utilized in cases where it is known to provide superior detection capabilities. To identify subsurface irregularities and flaws, a combination of immersion ultrasonic testing techniques is employed. By employing ultrasonic "A," "B," or "C" scans on welds, castings, forgings, and composites, we can identify defect indications that meet the highest inspection standards.
The process involves transmitting an ultrasonic wave into the material and analyzing the reflected wave. Skilled personnel can recognize flaws on the instrument screen, and specific characteristics of the flaw, such as its location, orientation, length, depth, and height, can be determined and evaluated.
Multiple ultrasonic testing companies specialize in providing only the Ultrasonic Testing. But, Globe Inspection & Engineering Consultancy has extensive expertise in this with advanced equipment for accurate and reliable detection of the defect. We always recommend engaging with one of the reputable ultrasonic testing companies that have a proven track record for ultrasonic testing services.
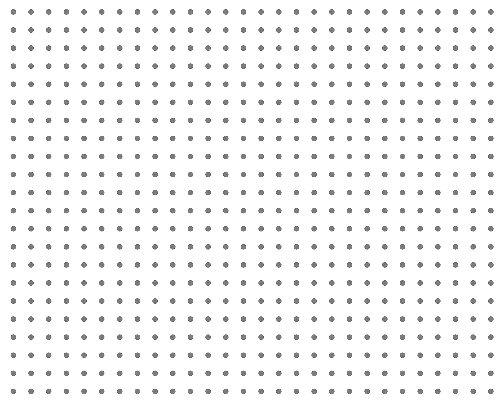
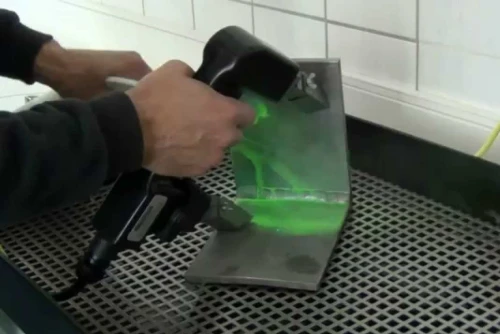
Magnetic Particle Testing (MPI)
Magnetic particle inspection is an effective technique for detecting surface and certain sub-surface defects in components made of ferromagnetic materials. The fundamental principles of magnetic particle testing (MPI) are based on relatively straightforward principles. Essentially, when a ferromagnetic component is magnetized, the presence of magnetic inconsistencies that are oriented approximately perpendicular to the direction of the magnetic field leads to the formation of a strong "leakage field." This leakage field is detectable both at and above the component's surface, and its presence becomes visible by the application of dry or wet magnetic particles that are suspended in a liquid medium. The magnetic particles gather at points of discontinuity that allow the detection of defects through the presence of magnetic particle testing.
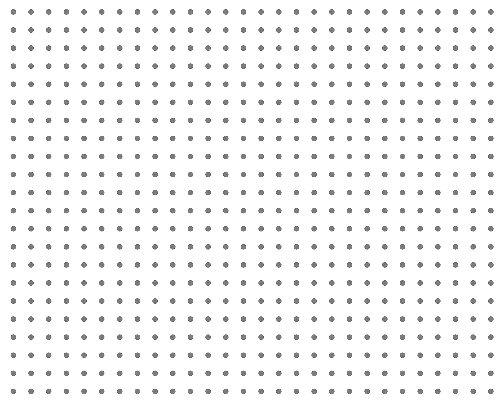
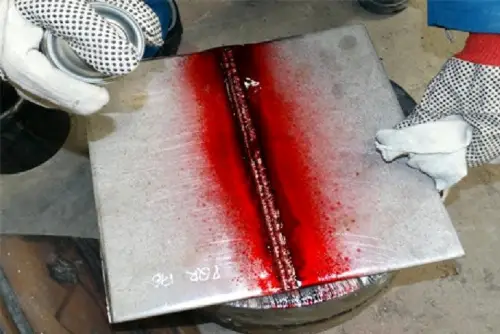
Liquid Penetrant Testing (LPT)
Liquid Penetrant Testing (LPT) is a testing method suitable for identifying surface-only defects on materials that are mostly impermeable. Also known as Dye penetrant testing, it is widely employed to detect flaws that break the surface in both ferrous and nonferrous components. Liquid Penetrant Testing can be conducted on-site or in a laboratory setting using either color contrast or fluorescent techniques. A vibrant-colored penetrant or fluorescent ink is sprayed onto the surface of the component being examined. The penetrant seeps into any surface imperfections or cracks. After removing the excess penetrant, a thin layer of developer is applied. This process causes the penetrant to be drawn out of the defects, making them visible when illuminated with visible light or ultraviolet light, as appropriate.
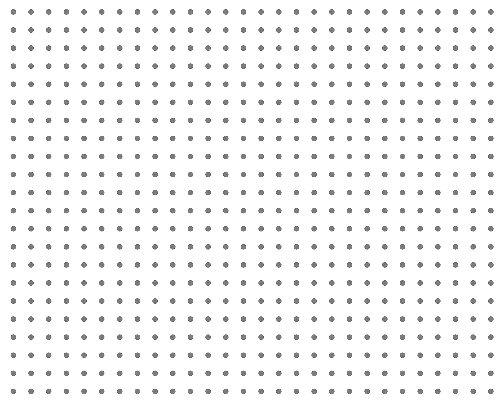
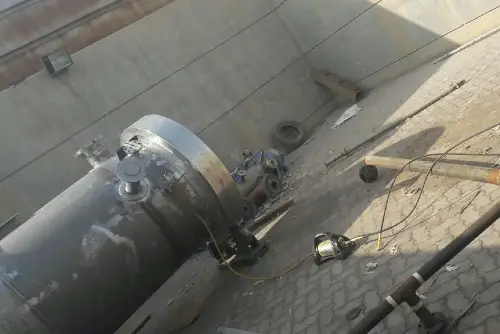
Radiography Testing. (RT)
Radiography testing is extensively employed to detect irregularities in various product types, primarily focusing on welds, castings, structures, and composites. In the energy sector, it is common to subject steel pipe weldments to testing methods to assess welding quality. One prevalent approach is a radiographic examination, which aims to capture images of flaws present in the welds. These flaws can originate from process defects such as porosity or lack of fusion, as well as from conditions that arise during service, such as corrosion-induced cracks. The radiographic inspection involves the use of radioactive sources like Ir-192, Se-75, or Co-60, as well as X-ray equipment for irradiation purposes. Our team of engineers, inspectors, and technicians possess extensive experience in handling these radioactive sources and X-ray equipment. Furthermore, we take pride in maintaining an impeccable safety record for all the projects we undertake, emphasizing the importance of Radiography Testing.
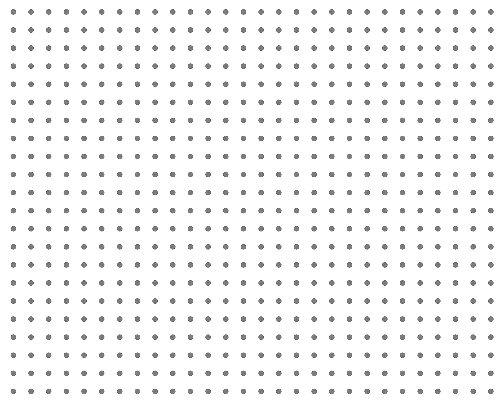

Visual Testing (VT)
Visual Testing (VT) is the most ancient and widely employed method among nondestructive testing (NDT) techniques. It serves as the initial stage in the inspection process for a range of product forms such as castings, forgings, machined components, and welded elements, as stated by the NDT Training & Test Center. In comparison to other methods, visual testing is cost-effective, straightforward to implement, and frequently obviates the necessity for additional testing methods. Several industries, including structural steel, automotive, petrochemical, power generation, and aerospace, rely on Visual Testing (VT) for their inspection needs.
Find out how we can help you bring quality improvements and potential to your products
FAQs
We have carefully compiled a list of frequently asked questions to provide you with the information you need about our NDT services.
Non-destructive testing (NDT) ensures the safety, functionality, and longevity of all critical assets in various industries. Non-destructive testing (NDT) prevents failures, accidents, and costly downtime of the assets by detecting defects, cracks, corrosion, and other anomalies in them.
There are a variety of defects that Non-destructive testing (NDT) detects. It includes cracks, porosity, lack of fusion, corrosion, weld discontinuities, material degradation, and others. Also, the technique identifies both surface and subsurface defects.